在近日于福州举办的“2009汽车制动器—制动器衬片行业发展研讨会”上,福建冠良汽车配件工业有限公司作为协办单位,介绍了其坚持创新、走可持续发展道路的成功经验。据悉,成立16年来,冠良立足高起点,坚持技术、工艺和管理创新,不断实现阶梯式跨越,进而稳居国内汽车摩擦材料行业领先地位。
推崇产品技术创新,赢取市场竞争发言权
冠良是印尼华侨独资企业,成立于1992年,翌年10月28日建成投产,开始生产鼓式刹车片。冠良启用的首条生产线,不仅具有与日本三菱建材公司技术合作的背景,而且采用了当时国内较为先进的热压工艺,其鼓式刹车片推出后,很快便凭借高品质和高起点迎来产销两旺。1998年,冠良与日本MK公司合作的盘式刹车片生产线宣告投产;2003年,冠良又引进日本华尔达技术,建成了离合器面片生产线。截至目前,冠良已形成了1万吨鼓式刹车片、300万套盘式刹车片、30万套制动蹄总成,以及1000万片离合器面片的年生产能力,产品享誉国内配套及售后市场,并大量出口北美洲、中东、澳大利亚及东南亚等国家和地区。
冠良总经理王长达表示,虽然公司在投产各类产品时,都引进当时较先进的技术和设备,但是,引进还要消化,模仿之后更要创新,才能确保产品处于市场竞争的战略高地。为此,冠良早在1997年筹备成立了摩擦材料研究所,先后投巨资购进了定速试验机、LINK蔡氏试验机、克劳斯试验机、LINK台架试验机、热膨胀试验机、压缩性能试验机等先进设备,并通过聘请国外资深专家及开展产学研合作等途径,增强技术创新的软、硬件实力。研究所成立以来,先后研究开发了37种配方,并有力支持了公司后来新增生产线的规划设计,以及原生产线的技术改造。其中,几年前成功研制的陶瓷配方摩擦片新品,也为冠良开启了新的业务增长空间。
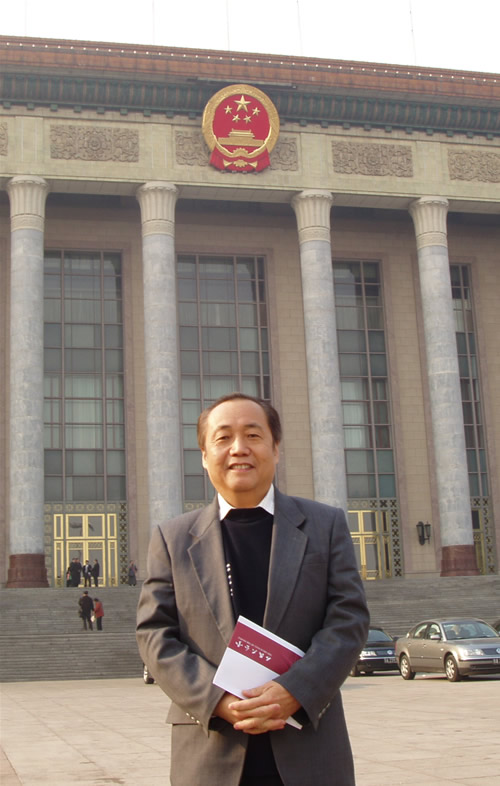
冠良总经理王长达
坚持生产工艺创新,夯实产品综合性价比
据王长达介绍,摩擦材料属于配方生产产品,很多技术诀窍都隐藏在生产工艺中。产品质量是否稳定,生产过程是否节能环保,都需要通过不断创新的生产工艺来保证。王长达说,以离合器面片为例,首先,一般采用湿式工艺生产的面片,需要采用大量的汽油(生产1吨面片,起码要消耗300公斤汽油),既浪费能源(汽油),又非常危险。而冠良的创新工艺则不需要使用汽油。其次,冠良无石棉缠绕式离合器面片,采用有别于现行工艺的辊压法生产,有效提升了面片的抗烧及耐磨性能,更好地满足了超载超限车辆对面片的特殊要求。
另外,在原先的离合器总成生产装配环节,总成厂收取离合器面片(未加工安装孔)后,通常自行冲、扩孔,容易破坏面片的平整度、残留毛刺,进而会影响离合器总成的外观及内在质量。为此,冠良率先在业内开发出独特的钻孔工艺,既保证了孔位、孔深的准确,又不会破坏面片的外观,使得总成厂更愿意采购带孔的面片。一方面,总成厂可省却加工孔的生产环节,以提高流水线生产的效率;另一方面,又能避免自行加工导致的废品率,有助于变相降低离合器总成的生产成本。王长达认为,其离合器面片产品自投产以来,之所以能取得产销量连年快速递增的业绩,在很大程度上得益于其对面片开展的一系列工艺创新。
在参观车间的过程中,作为参与公司筹建,并引领冠良跻身国内摩擦材料行业第一梯队的业界资深专家,王长达如数家珍地向记者吐露了冠良无处不在的创新理念。例如,如何通过采取预混料、双层料、正模及高效节能烘干等技术,让有16年历史的老生产线(鼓式刹车片)始终焕发青春活力;如何通过导入一次成型的正模热压及正模温压工艺、电脑自动配料系统及静电喷粉涂装等设备,使得冠良盘式刹车片能向国际先进水平看齐……。王长达认为,面对激烈的国内外市场竞争,唯有创新,才能使企业冲出重围;唯有创新,才能使企业保持活力;唯有创新,才能使企业实现可持续发展。