杜鹏 刘辉 毛英慧
长安大学汽车学院
[摘要] 利用有限元软件ABAQUS,对装有ABS的盘式制动器在不同附着系数路面的紧急制动过程中制动盘的动应力分布进行了分析和研究。通过动应力特性的对比分析,得出了在高低附着系数的路面制动盘的应力分布。
[主题词] ABS 盘式制动器 有限元 ABAQUS
0 引言
制动防抱死制动系统(Antilock Braking System,ABS)是在制动过程中防止车轮被制动抱死,提高汽车的方向稳定性和转向操纵能力,缩短制动距离的安全装置。未安装防抱死制动系统的车辆在紧急制动时,不可避免地会出现车轮在地面上抱死拖滑的现象,地面所能提供的侧向附着力很小,车辆在受到任何微小外力的作用下就会方向失稳,极易发生交通事故。在潮湿路面或冰雪路面上制动时,这种方向失稳的现象更加严重。
盘式制动器在紧急制动过程中对不同附着系数路面所受的制动力或制动力矩是不相同的,其应力场分布也必然不同。由于应力分布的不同会影响到制动器的制动效能,从而影响汽车行驶的安全性,因此在ABS作用下,对不同道路状态下制动盘的动应力进行研究,具有一定的现实意义。
本文以某小型轿车为例,对其在36km/h速度下,在高、低两种附着系数路面上进行紧急制动时,对浮钳盘式制动器的制动盘应力特性进行了有限元分析。
1 制动盘的受力分析
浮钳盘式制动器的受力如图l所示,制动摩擦副中间的旋转元件是圆盘形制动盘,制动盘在半轴的带动下一方面沿车辆行进方向作直线运动,另一方面绕半轴作旋转运动。制动时,活塞3受油缸液压力的作用推动制动摩擦片沿轴向移动,以一定的压力p1压向制动盘。作用在制动钳体l上的反作用力p2推动制动钳体向右移动,使制动摩擦片2压靠到制动盘4上。制动盘两侧的摩擦块在p1和 p2的作用下夹紧制动盘,使之在制动盘上产生与运动方向相反的制动力矩,促使汽车制动。
紧急制动时,高附着系数路面ABS的制动压力曲线如图2所示,可以认为ABS系统此时不起作用。在低附着系数路面,制动压力达到最大值后,由于ECU(电子控制单元)的控制,制动力会在车轮即将抱死时迅速下降,然后再上升,如此反复,从而达到防抱死制动的目的,如图3所示。
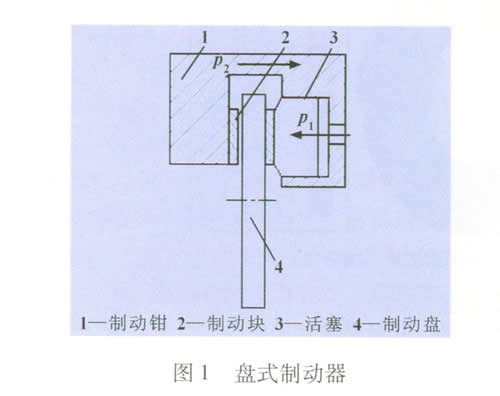
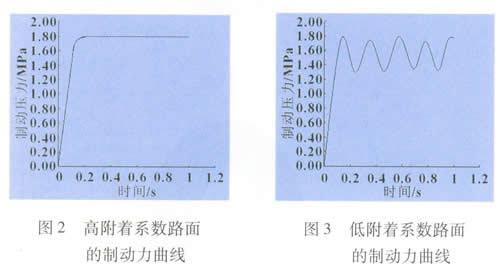
2 有限元模型的建立
2.1 有限元网格划分
采用的制动盘为双侧摩擦面制动盘,两个摩擦面通过呈圆周阵列分布的轴向空心柱体散热筋连成一体。图4为制动盘简化后的几何模型。
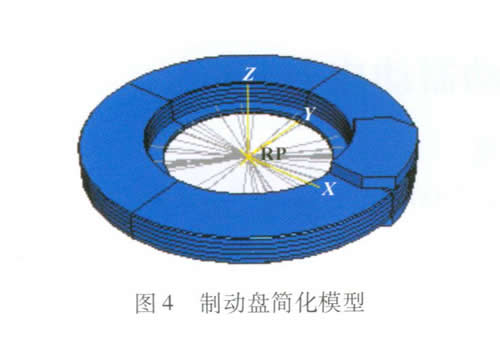
2.2 模型的材料特性
制动盘的材料是Ht250,弹性模量为1.55×108 MPa,泊松比为0.27,密度为7340kg/m3,抗拉强度为220MPa。制动块的材料是树脂加强复合材料,弹性模量为2.2×1010MPa ,泊松比为0.25,密度为1550kg/m3。
2.3 模型的边界条件和加载
在制动器起作用前,为了保证车辆的正常运行,制动盘与制动块之间存在一定的间隙。此时刹车片固定不动,制动盘在半轴的带动下向前运动,并高速旋转。因此,赋予制动盘和半轴耦合点一个转速和一个向前的速度。由点带动制动盘实现其运动状态模拟。当速度达到36km/h时,开始对制动块加载。此处载荷以均布压力的形式施加到制动盘表面上。载荷的大小根据制动力矩、摩擦片面积计算得出。试验路段附着系数分别为0.8和0.15。两种工况下压力的变化曲线如图2、3所示。制动盘与制动块接触面之间摩擦系数为0.37,制动片面积为0.004m2。为便于计算,模型忽略了汽车行驶时由振动引起的位移误差。
3 计算结果及分析
根据试验车辆实际测得的制动力矩曲线,计算分析时间取为1s,即车辆在1s内完成整个紧急制动过程,取计算步长为0.0ls。
两种工况下计算得出的von Mises应力(即根据第四强度理论换算的等效应力)云图,如图5、6所示。可以看出,在相同的制动过程中,ABS作用时的低附着系数路面制动时,制动盘所受的应力水平总体上大于高附着系数路面制动时所受的应力。
由图5可看出,在制动初始阶段,两盘上的应力分布规律和变化趋势基本相同。但在0.15s时,制动力达到最大值后,两盘面上的应力分布有很大差别,如图6所示。在高附着系数路面制动时,由于制动力一直保持在最大值附近,制动盘很快进入抱死状态。因此,制动盘只在接触区域的应力较大。在低附着系数路面上制动时,由于ABS的作用,整个制动过程中制动盘保持旋转,制动盘与制动片相接触的区域是在变化的,使得应力分布更加均匀。
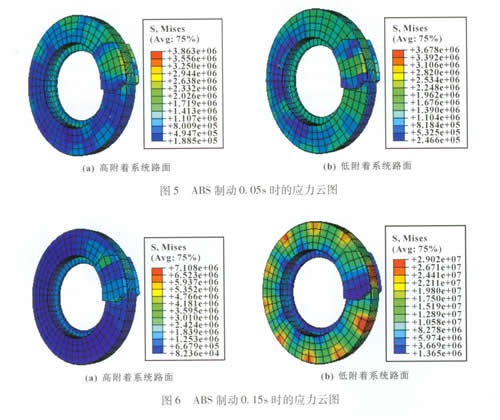
4 结论
车辆制动器系统制动过程是一个接触摩擦问题,通过ABAQUS有限元分析软件,对在不同附着系数路面的紧急制动时制动盘的动应力分布进行了研究。结果表明,在低附着系数路面,ABS的应用虽使制动盘的局部应力有所增加,但整个制动器的动应力分布更加均匀,更有利于结构的安全。