前轴总成对汽车制动跑偏的影响分析及其改进措施
【摘要】 汽车制动性能良好是汽车安全行驶的重要保证。汽车在行驶过程中因制动跑偏而导致车祸,是许多交通事故主要原因之一。了解、分析汽车制动跑偏的主要因素,迅速地找出故障原因,给予排除以确保行车安全。首先分析汽车制动跑偏的主要原因,然后重点分析前轴总成对汽车制动跑偏的因素和在生产过程中的改进措施。
关键词:前轴总成;制动;跑偏
1 概述
一段时间市场(用户)强烈反映某公司生产的STB/MAN前轴总成跑偏严重,影响该公司声誉和市场份额,要求相关部门组织解决。该公司组织攻关小组,对前轴质量进行跟踪分析,并对其提出整改措施。
影响汽车制动跑偏的因素比较多,比如:汽车车架变形,将造成车辆轮荷分布不均;两侧轮胎气压不相等;前后轴移位;减振器失效;悬挂系统设计有问题或悬挂受伤、变形、移位等诸多因素。
前轴总成零部件制造和装配质量的好坏是影响汽车制动跑偏诸多因素中最重要的一项。一般情况下,前轴总成有以下几方面对汽车制动跑偏影响很大:⑴ 左、右制动器产生的制动力不相等;⑵ 轮毂轴承预紧力偏小;⑶ 前轮定位参数不准确;⑷ 转向系相关零部件间隙比较大,刚性不好。以下就对这四点逐一分析,并提出整改措施。
2 左、右制动器产生的制动力不相等
2.1 原因分析
汽车行驶过程中是靠制动器与地面产生的一个与行驶方向相反的外力来实现停车或减速的,这个与行驶方向相反的力称为制动力。制动力主要取决于制动器内制动摩擦片与制动鼓的摩擦力。如果汽车在制动过程中,前轴左、右制动器产生的制动力大小不等或同一时间内制动力增长速度不一致,必然造成制动跑偏。
这种现象在道路试验过程中主要表现为紧急制动时,一侧车轮已经抱死,另一侧车轮只是减速而不能抱死。汽车偏驶向车轮抱死一侧,从制动轮与地面的拖痕来看,可见到一边拖痕很深而另一边拖痕很浅,甚至没有拖痕。经过把跑偏的前轴放在该公司制动器磨合检验台上检验,可以看到在制动过程结束时,左右制动轮产生的最大制动力的差值很大,一般左右两边的制动力差大于20%(工艺要求左右两边的制动力差小于8%)。
造成这一结果的主要原因是:⑴ 某一制动气室膜片破裂、制动分泵密封圈损坏等质量问题;⑵ 某一制动气室推杆变形或卡死或制动分泵活塞发咬,不灵活;⑶ 某一制动凸轮轴动作不灵活,间隙调整臂损坏;⑷ 制动蹄支承销与制动蹄发咬,不灵活;⑸ 左、右制动器与蹄片间隙大小不等;⑹ 左右制动器摩擦片材料不同、厚薄不均、摩擦系数不同等;⑺ 某一制动摩擦片有油污等;⑻ 旋转件(轮毂和制动鼓)静平衡不好;⑼ 制动鼓严重失圆;⑽ 轮毂大平面与中心轴线垂直度超差。
2.2 解决措施
对于2.1中的⑴、⑵主要措施为加强对供应气室厂家的考察和加大外协检验力度,保证合格的气室,要求在同一厂家的制动气室必须装在一根前轴上。
对于2.1中的⑶、⑷主要措施是:在装配过程中,制动凸轮轴、制动蹄片支承销上面喷涂防卡滞剂,防止配合件相互粘合。并且100%检验是否转动灵活。
对于2.1中的⑸,这是由于转向节、制动底板、轮毂、制动鼓、制动蹄、气室支架和制动凸轮轴等相关零部件在机械加工没有满足图纸设计要求造成的。若将其装配在前轴总成上,公差累积必然造成一侧的两制动蹄与制动鼓间隙大小不等,汽车在制动过程中,一侧的两个制动蹄因不能完成与制动鼓接触,从而导致产生的制动力不足,若另一侧产生的制动力与其不相等,汽车在制动时将产生跑偏现象。为了使两侧的制动器产生相同并比较大的制动力,经过工艺改进采用以下措施:
⑴ 对于MAN前轴总成,2008年之前采用制动蹄与制动底板加工成成品,由装配车间装配,因制造精度满足不了图纸,装配成总成后,前轴的一侧的两制动蹄与制动鼓的间隙差一般情况都大于0.3 mm,不能满足工艺要求。之后,进行工艺改进,由华臻公司对成品制动底板和半成品制动蹄先装配成一个制动器总成,然后加工制动器总成(如图1所示),最后由该公司转配,通过工艺改进,前轴的一侧的制动蹄与制动鼓的间隙差一般情况都不大于0.2 mm,满足了工艺要求,提高了生产效率。
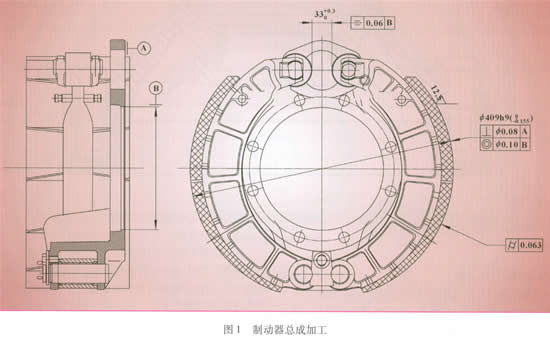
⑵ 对于STR前轴总成,用制动蹄合车工具100%合车制动蹄,保证轮廓垂直度均小于0.1 mm,同时左右制动鼓与制动摩擦片间隙大小相等;并对一侧的制动器的两个制动蹄与制动鼓的间隙差控制在0.3 mm内。为了使两侧的制动蹄合车的外径保持一致,特要求一把制动蹄合车工具合车一根桥的两侧制动器。另一方面,改进制动蹄合车工具,确保制动蹄总成质量。
对于2.1中的⑹,要求在装配过程中,同一厂家同一批次的制动蹄才能装在一根前轴总成上,这样才能消除左右两边制动器因摩擦片材料引起摩擦力不相等。
对于2.1中的⑺,若一边的制动蹄摩擦片上有油物,则这边汽车在制动过程中,制动力将会下降,从而导致两侧制动器产生的制动力不相等。在装配车间严格要求工人在装配过程中,不允许将任何油污落在制动蹄上,并要求装配工人随时更换干净的手套进行作业,避免在制动蹄摩擦片材料粘抹油物。
对于2.1中的⑻,要求外协厂家100%对制动鼓做静平衡试验,严格保证质量。
对于2.1中的⑼,不但要求控制制动鼓质量,同时还要求在桥总成装配线对制动鼓100%检测Φ420(STR前轴)或Φ410(MAN前轴)内圆面的跳动,保证在0.15mm以内。
对于2.1中的⑽,如果对轮毂大平面检测跳动比较大,将造成制动过程中制动鼓与制动蹄只接触两边,从而导致这一侧的制动力不足。造成轮毂大平面检测跳动超差,一般是压装轮胎螺栓时造成的。2007年以前压装轮毂轮胎螺栓时,在轮毂大平面下没有垫铁,在压装轮胎螺栓时,因轮胎螺栓与轮毂的孔的配合公差不可能完全一致,在压装过程中两边受力不相等,将造成轮毂大平面跳动超差。2007年后,对压装工艺进行改进,在轮毂底部垫一垫铁(如图2所示),这样就解决了压装变形的问题。在装配线对轮毂装配完成后,检测轮毂大平面跳动,一般都在0.10mm以内。
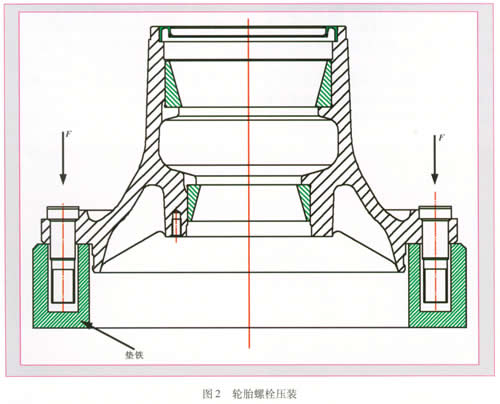
3 轮毂轴承预紧力不够
轮毂轴承预力不够,则造成在汽车制动过程中,轮毂的支撑刚性不够,容易造成跑偏打摆现象。经过现场工艺调整,轮毂轴承预紧力由16~30N变更为30~50N(用弹簧秤检测)。
4 前轮定位参数不准确
前轮的外倾角、主销后倾角、主销内倾角和前束值不正确也将对车辆行驶的安全性和经济性产生直接的影响,破坏了汽车行驶的稳定性,在制动时也将造成制动跑偏。在道路试验过程中可以发现制动跑偏的方向不是固定不变的,而是时左时右的,这类前轴总成在该公司制动器磨合检验台上检验时左右两边的制动力没有明显的变化,一般左右两边的制动力差在8%之内。
解决措施:
⑴ 前轮的外倾角、主销后倾角、主销内倾角主要通过公司的零部件机械加工保证,提高前轴的主销孔的角度加工精度,提高产品质量。
⑵ 前束的测量和调整一直是桥装配线重点工位,现在使用数显式测量工装代替普通的米尺测量,保证了测量数值的准确性。
5 转向系零件的间隙比较大(刚性不好)
转向系的好坏也将影响到汽车的直线行驶,如果各连接件间隙过大,将引起汽车在制动中摆头跑偏,不能保持正常的运动轨迹。前轴总成转向系间隙比较大,刚性不好,主要包括:转向横拉杆紧固不牢固;转向节与推力轴承的间隙大;主销与衬套配合间隙大。
5.1 转向横拉杆紧固不牢固
转向横拉杆紧固不牢固,连接刚性降低,也会对制动跑偏产生一定的影响。最严重的是横直拉杆球头销松推,将造成汽车在制动时严重跑偏。造成这样主要有两方面原因:① 转向横拉杆的球头销与转向横拉杆臂配合的锥面孔配合不好,不能使两锥面完全贴实;② 在装配过程中,紧固转向横拉杆球头销的螺母没有拧紧,不能确保转向横拉杆的球头销与转向横拉杆臂配合的锥面是否贴实。
解决措施:
⑴ 对于①主要是加大外协检验力度,提高转向横拉杆的球头销锥面与转向横拉杆臂锥面的精度。
⑵ 在装配过程中,紧固转向横拉杆球头销的螺母要求100%检验拧紧力矩,满足工艺要求。
5.2 转向节与推力轴承的间隙大
转向节与推力轴承的间隙大,造成汽车在制动时,转向节将上下窜动,刚性必然会降低,从而使汽车在制动时产生打摆跑偏现象。造成原因主要有:①推力轴承上面的包铁皮影响测量间隙数值的准确性;②调整垫片规格比较少,装配工人不容易调整;③装配工人没按要求装配,不能满足工艺要求。
解决措施:
⑴ 对于①,改进推力轴承结构,取掉上面包铁皮(如图3所示),使测量转向节与推力轴承的间隙测量更为准确,减少了包铁皮的影响,提高了检测的精度。
⑵ 对于②,增加调整垫片种类,使原来0.1 mm一档的规格变成0.05 mm一档,便于调整。
⑶ 对于③,在前轴装配中,则要求加大检验力度,严格保证工艺要求。
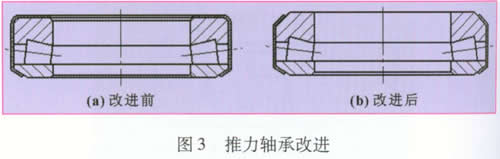
5.3 主销与衬套配合间隙大
主销与转向节衬套配合间隙过大,将引起汽车在制动中摆头跑偏,不能保持正常的运动轨迹。解决措施就是严格控制主销和衬套的公差尺寸,提高产品质量。
6 结论
经过这几年的持续措施整改,使该公司的前轴跑偏率明显下降。但因引起汽车前轴跑偏因素很多,只靠车桥厂一家攻关是不够的,下一步笔者认为整车厂对车架和悬架部分质量也应下力气跟踪解决,以便公司彻底根治汽车跑偏现象。