商用汽车前盘后鼓气压制动系统的协调性
孙龙
中国汽车技术研究中心
徐达
武汉理工大学汽车学院
【摘要】本文对比分析了盘式制动器和鼓式制动器的结构特点和性能差异。随着我国汽车相关标准法规的逐步制定和执行,商用汽车制动系统采用前盘后鼓制动形式的配置已成为标准配置,本文重点对该种配置所带来的制动协调的技术要求和目前在应用中存在的问题作了分析。
【关键词】盘式制动器,鼓式制动器,商用汽车,制动系统
1.前言
随着汽车技术的不断发展,盘式制动器相对于鼓式制动器有许多突出的性能特点,特别是抗热衰退性能,已在欧洲等市场得到了广泛应用。尽管多年前国内主要中重卡车生产企业就已开始对盘式制动器的应用进行探索,做了许多的研发工作;但是直到2012上半年,除了个别汽车生产企业在前桥上有一些小批量使用外,其他主流企业均未形成有效的批量使用。从技术和市场的角度来看,盘式制动器取代鼓式制动器应是必然的趋势,欧洲卡车发展的历程已经验证了这一点。
考虑到盘式制动器在汽车制动主动安全性方面的明显优势,我国工信部、公安部、工信联产业于2011年底联合下发了第632号文,其中明确要求危险品货物运输车、专用校车和车长大于9米的公路客车、旅游客车的前轮必须安装盘式制动器。新版GB7258 -2012《机动车运行安全技术条件》中明确规定危险货物运输车的前桥和车长大于9m的客车前桥应装备盘式制动器)以及GB 24407-2012《专用校车安全技术条件》中规定专用校车前轮应安装盘式制动器)。相关的商用汽车企业在国家强制性标准法规要求的情况下对装备盘式制动器开始有了一定规模的应用。
2.商用车制动系统中的制动器
2.1 商用车常用制动器分类及结构
制动器主要根据摩擦的工作表面分为盘式制动器和鼓式制动器(图 1)。盘式制动器以平面摩擦为制动工作表面,而鼓式制动器以圆柱面摩擦为制动工作表面。
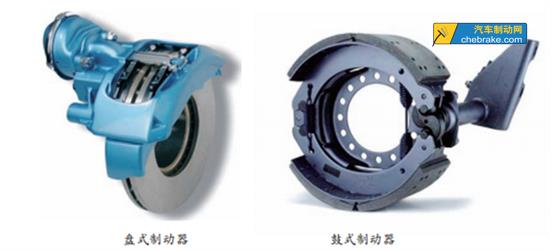
图 1 盘式制动器和鼓式制动器
2.2 盘式与鼓式制动器的性能对比
不同的制动器形式,决定着制动性能会各不相同。有研究结果证明,盘式制动器优势明显,尤其是在控制精度和制动稳定性上明显优于鼓式制动器,如果将制动防抱死ABS、电子制动系统EBS,以及电子稳定系统ESP与盘式制动器配合使用,其控制精度和效果则会更佳;当然,盘式制动器热容量小、温升快是其结构决定的不容回避的问题。如图 2所示为对20′的盘式、鼓式制动器进行试验,获取了不同温度和不同制动次数情况下制动力矩的变化曲线。
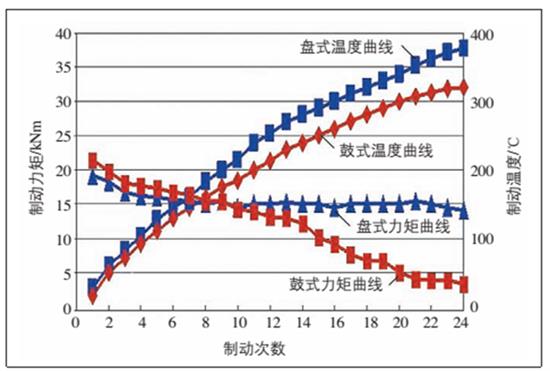
图2制动力矩变化曲线
盘式和鼓式制动器在相同的制动工况下有显著的性能差异。与鼓式制动器相比,盘式制动器的最大优点是制动稳定性好,制动性能受外界影响小。盘式制动器允许的工作温度高,制动盘通风冷却较好,带通风孔的制动盘散热效果尤佳,直接把热量散发到空气,对轮毂温度升高影响不大。更换盘式的摩擦片容易,维修简便,甚至可以在现场进行,而对鼓式的类似的作业则复杂得多。新的盘式制动器装车后磨合的里程也比鼓式的要少许多。表 1为从7个方面对这两种形式的制动器进行考量、加以比较。
从表 1可以看到,2种制动器在制动力矩、稳定性、自质量和成本等方面相比较,盘式制动器优劣对比为5:2,其优势十分明显。
用制动器效能因数与摩擦系数的关系曲线来说明两种结构制动器的效能及其稳定程度,见图 3。
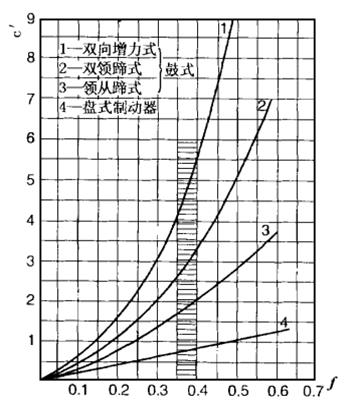
图 3 盘式和鼓式制动器效能因数与摩擦系数的关系
盘式制动器的制动效能比鼓式制动器小,它的稳定性最好。为了弥补制动效能小的问题,一般盘式制动器都采用大直径制动分泵,且加装助力装置,使之具有较大的制动效能。
迟滞性能是衡量机械装置传动效率和重复性能优劣的一个重要指标,由于盘式制动器直接由制动缸驱动衬片压向制动盘,省却了鼓式制动器中的制动凸轮轴、推杆及制动缸支架,传力部件少,受力简单,反应灵敏,迟滞量仅为10%,而鼓式则为30%,这也是盘式制动器制动响应快且效能稳定的结构保障之一(见图 4)。
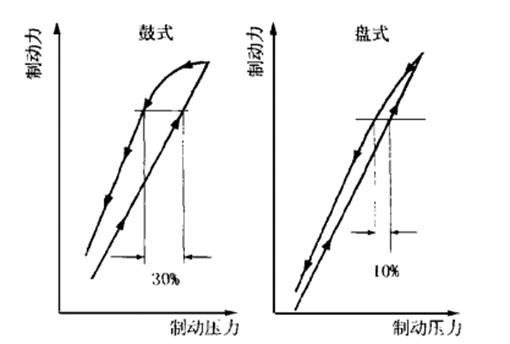
图 4 盘式和鼓式制动器的迟滞特性
由此可见,盘式制动器在汽车制动性能的三项评价指标即制动效能、制动效能的稳定性以及制动时汽车的方向稳定性上比鼓式制动器具有明显的优势。
2.3气压盘式制动器的特点
由于自身的结构特点,鼓式制动器在工作时产生的热量较难散发。其摩擦造成偶件即制动鼓热变形较大,受热后制动间隙也随之增大,因而引起气室推杆行程的增加。延长制动反应时间甚至引起气室推力下降从而降低制动能力;此外由于鼓式制动器受热后压力分布变化较大,还会带来制动效能下降,磨损加快的一系列的问题。而气压盘式制动器由于制动盘大部分都暴露于空气中,热交换容易,工作时散热较快:且制动盘受热时变形不会引起压力分布变化,对制动间隙的影响是负向的,因而盘式制动器的制动效能非常稳定,制动可靠性高;且制动反应时间较短。这一点对于匹配ABS、ASR、EBS等电子控制装置具有较大的意义。
由于气压盘式制动器的促动力来源是压缩空气,通过杠杆作用的转换,相对于液压盘式制动器能够产生大得多的制动输人力。驻车制动的形式也可以做得和鼓式制动器一样简单;也根本不存在气阻现象,因而克服了传统的液压盘式制动器的缺陷;同时由于制动间隙较小且传动效率较高。再加上制动间隙自调机构的作用。使盘式制动器所消耗的空气量比鼓式制动器小得多,制动反应时间也相应缩短。制动气室也可以始终工作在最佳推杆行程内。
使用气压盘式制动器在所需制动力矩相同的情况下,其外形尺寸比鼓式制动器小得多.因此给整车布置带来了方便;而且由于其质量特别是旋转部分的质量小很多,失衡量也小得多。使非簧载质量大为减轻,加上失衡量减小,可以明显改善汽车的舒适性、平顺性和操纵稳定性。
由于气压盘式制动器的摩擦衬片可磨损厚度达20mm,而鼓式制动器的可磨损厚度摩擦片不到10mm,因此在同等使用条件下,盘式制动器摩擦衬片的更换周期较鼓式制动器长。如果考虑到两种制动器散热能力的差别,它们的更换周期差别能达到3倍以上;此外,盘式制动器更换摩擦衬片时只需要扒掉轮胎即可。而鼓式制动器更换摩擦片则复杂得多,工时及材料消耗也大大超过盘式制动器。而且盘式制动器的制动间隙不需要通过手工调整,摩擦片磨损到规定厚度时,还会自动报警;这些优点可以使用户节约日常维护的时间;制动器散热能力的提高也可以降低轮毂及轮辋的温升,从而大大延长轮胎的使用寿命。所以对用户来说,使用气压盘式制动器所带来的效益要大于增加的成本。
3. 盘式制动器在商用车上的应用
据不完全统计,盘式制动器在欧洲得到了广泛应用,其应用比例仍在持续增加(表 2),在北美和除中国之外的亚洲其他国家也有一定的增长比例,但中国商用车仍然以鼓式制动器为主,盘式制动器的应用明显低于其他地区。
表 2 国内外中重卡制动器应用比例对比
区域 |
欧洲 |
北美 |
亚洲 |
中国 |
鼓式制动器 |
<15% |
约80% |
≥90% |
约97% |
盘式制动器 |
≥85% |
约20% |
<10% |
约3% |
盘式制动器产品技术先进性明显,可靠性总体良好,具有创新性和技术标准的集成性。欧美国家自20世纪90年代初开始将盘式制动器用于大型公交车,到2000年,盘式制动器(前后制动均为盘式)已经成为欧美国家城市公交车的标准配置。我国从1997年开始在大客车和载重车上推广盘式制动器及ABS防抱死系统,但因进口产品价格太高,主要用于高端产品。2004年交通部强制在9m以上高Ⅱ型客车上“必须”配备后,盘式制动器才得以应用。目前国内知名的大型客车厂家均已在批量生产带盘式制动器的高档客车。此外,盘式制动器在北京、上海、广州、深圳、武汉等城市的公交车上也得到了大量应用。对于重卡而言,盘式制动器作为应用型新技术,也已经是成熟产品。目前国内重卡生产企业均完成了盘式制动器在重卡上的前期试验及技术储备工作,盘式制动器在某些方面将成为未来商用汽车制动系统匹配发展的新趋势。
4.商用汽车制动系统前盘后鼓的配置
4.1驻车制动对前盘后鼓配置的要求
由前桥的盘式制动器和后桥的鼓式制动器担负主要的行车制动功能,同时后桥的鼓式制动器还担负驻车制动功能,这也是“前盘后鼓”的配置得以先行应用的主要原因之一。在汽车底盘未作改进情况下,便可直接实现。如果要在车辆上实现“前盘后盘”的配置,即后桥上要安装带驻车制动功能的盘式制动器,则底盘的结构也要作相应变化,因为许多现用的底盘和桥正好没有安装盘式制动器驻车制动机构的空间,受结构的影响,盘式和鼓式制动器的驻车制动驱动机构的布置正好相差90°。对于浮动钳结构盘式制动器,其同一种制动块可兼用于行车和驻车制动,而固定钳盘式制动器为了实现驻车制动,必须在主制动钳上另外附设一套用作驻车制动的辅助制动钳。在轿车的后桥上,有带鼓式驻车制动器的盘式制动器,但这种“盘中鼓”结构过分复杂紧凑,且维修调整不便,成本高,因此这种结构在重型汽车上没有应用。
4.2前盘后鼓制动器前后制动时间的协调
大中型商用车底盘一般采用气压制动,鼓式制动器以领从蹄式制动器为主。盘式制动器与鼓式制动器由于其结构形式和作用方式的不同导致在制动作用时间上存在较大差异。目前,国内使用的盘式制动器的制动间隙为0.2-0.5mm(每边),鼓式制动器一般为0.4-1mm。从鼓式制动器和盘式制动器的结构看,鼓式制动器的零部件存在的间隙以及行程都要比盘式制动器大,所以制动器作用时间要大于盘式制动器,而且在相同时间内制动磨损量也不同,这就导致了在制动过程中,两者从制动初期到制动中后期会有很大的差别。行车制动器的磨损随着车辆行驶里程的加大而增大,但前轮的盘式制动器的磨损间隙是能自动调整的,而后轮的鼓式制动器若不装自动调整臂则不能自动调整磨损间隙,这种配置的不一致或不协调,会造成前后轮制动器制动间隙的差异越来越大,降低了车辆的制动性能,形成恶性循环,引发重大交通事故。
原先国产客车的制动系统都是以前后鼓式制动器进行设计的,如果只是简单的将鼓式制动器换成盘式必然是盘式制动器先于鼓式制动起作用。由于制动时间的不同步会出现前轮先于后轮抱死的时间大大提前。当进行紧急制动时,由于前制动的提前,即使发动机不再进行动力输出,在惯性力的作用下,后轮还是起到驱动轮的作用,制动起作用瞬时车速相对较高,盘式制动先于鼓式制动起作用,制动盘与制动摩擦片产生相对高速滑移,直至鼓式制动器参与工作,这就造成了制动盘与摩擦片的磨损。随着制动的频繁增加,这种磨损的影响会越来越大,最后导致整个制动系统不能满足国家法规最佳制动效能。在轻微制动时,盘式制动器的回位弹簧力一般小于100N,而鼓式的则要比其大几倍,盘式制动反应速度要快于鼓式制动,承担了较多的制动力矩,同时制动回位时也会出现滞后鼓式制动器,使其制动磨损增加,这在公交车上反映特别明显。试验证明,盘式制动器的摩擦片在频繁制动的情况下,其寿命会缩短3-4倍。针对上述情况需要对制动管路进行重新布置。对大部分客车制动系统来说由于后制动管路较长,为了使后轮制动与前轮制动尽量同步,多采用在后制动管路中安装继动阀,这样虽然在一定程度上避免了后制动作用时间与前制动时间出现大的差异,但是对于前盘后鼓的配置形式显然满足不了要求。
为了使商用汽车气压制动系统的前盘后鼓配置形式在制动反应时间尽量协调一致,提出如下技术要求和改进措施:
1)对于具有前盘后鼓气压制动系统的商用车辆,一定要标准配置自动调整臂。不能装手动调整臂。
2) 在布置允许的情况下将后储气筒后移,继动阀尽量靠近后制动器布置,减少后制动管路的折弯数目,合理选取前后制动管路长度。
3) 利用制动阀的工作原理来实现缩短后制动反应时间的目的。制动阀上下压力差越大,后制动反应时间越快,可以采用上下腔压力差大的制动阀,使后制动反应试验相应提前。
4) 采用气压计量阀串联于前制动管路,只有当前制动气压达到一定值时计量阀才开启,这样就延缓盘式制动的时间。同时,根据需要在前制动气室安装快放阀,快速解除制动,使前轮恢复转向功能。
5) 与ABS配合使用。与ABS配合使用更能体现盘式制动的优越性。
4.3盘式与鼓式制动器结合的问题
盘式制动器在载货车上应用之初,各汽车厂商曾对新车设计时前后桥全部装用盘式制动器还是采用“前盘后鼓”配置有许多争论,但在重型车上各厂家几乎无一例外地首先采用了“前盘后鼓”的方案,这主要考虑以下几个因素:
1) 重点解决法规限定后桥轴荷后,为提高车辆总质量而增加前轴负荷以及车辆平均车速提高后所带来的制动负荷大幅上升的制动稳定性及前轮制动发热爆胎的问题;
2) 带驻车制动功能的盘式制动器在现有商用车底盘上的安装有一些在布置空间上的困难;
3) 初装盘式制动器的价格过高。从理论分析和实际试验结果都表明全盘式制动器配置的车辆才具有最理想的综合制动性能,尤其对汽车列车更是如此,这是一种发展趋势。最近在欧洲的一次展览会上,已有一半的挂车采用了盘式制动器,预计三年内欧洲将有70%的挂车装用盘式制动器。这一趋势与全盘式制动器的主车发展步调一致,让用户在使用中获得最佳的经济和安全效益。
目前,前盘后鼓的配置形式已成为国家法规要求的主要形式,但在实际应用中,由于前桥的盘式制动器的制动间隙是自动调整的,而后面的鼓式制动器的大多数使用的是手动调整臂,即制动器的磨损间隙不能自动调整,造成了前面自调后面手调的不合理的配置。
对装有手动调整臂的车辆,在实际运行中,有不少司机一是不去调,二是不会调,其结果是不调。这样使得前盘后鼓配置的车辆在运输过程中,随着运输里程的加大,其制动不协调性越来越明显,甚至引发重大交通事故。因此使前盘后鼓配置这一促进汽车制动技术进步的事反而带来了负面的影响。
在GB 12676-1999 《汽车制动系统结构、性能和试验方法》以及报批的GB-2013《商用车制动系统技术要求及试验方法》中,已明确规定对N2类和N3类中重卡货车O3类和O4类中重型挂车,必须要有行车制动磨损间隙自动调整装置。若上述车型的汽车生产企业以及车辆公告和车辆运输的管理部门严格地执行了上述的国家强制性标准,就不会出现在前盘后鼓车型中前面自调而后面手调的不合理的配置。
5.结论
随着国家相关标准法规的颁布,比如新版GB7258-2012《机动车运行安全技术条件》和GB24407-2012《专用校车安全技术条件》以及报批的GB-2013《商用车制动系统技术要求及试验方法》等标准的推进,未来几年,盘式制动器在我国将会得到更加快速的推广和应用。它在重型车上的应用更具紧迫性,“前盘/后鼓”的配置也将是重型车底盘和制动系统近几年的重大变化,前盘后鼓布置形式可扬长避短,能充分发挥盘式制动器的优势。世界汽车技术的发展为我们提供了解决重型车前轴制动问题及轴荷问题的途径,它既是重型载货车底盘技术发展的一种趋势,更是车辆全面满足制动安全及轴荷法规的需要。